From theory to practice: Optimizing grain size measurement with MiViA in cold-rolled strip production
Discover in our blog post how grain size measurements are carried out and interpreted in cold-rolled strip production and learn more about the importance of microstructure images for quality assessment.
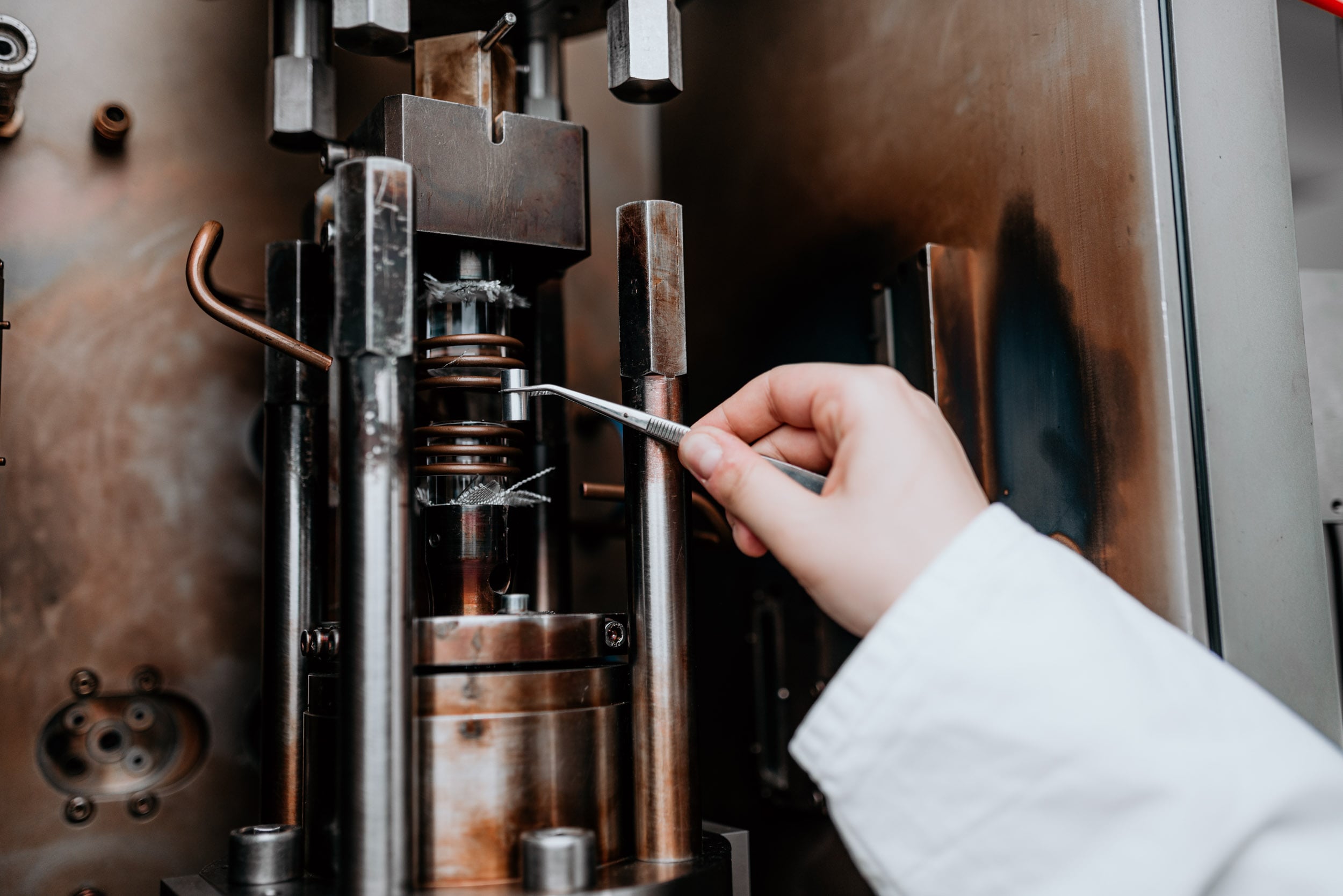
Navigation
Effects of grain size on the quality of the cold-rolled strip
In cold strip production, metal strips are processed by rolling at room temperature, which results in more precise dimensions and better surface quality compared to hot rolling. These strips are widely used in sectors such as automotive, construction, electronics and household appliances. The high precision and quality of the end product are crucial for the performance and durability of the products made from it.
The grain size of the metal, i.e. the size of the individual crystals within the metal structure, has a significant influence on the mechanical properties of the end product, such as strength, hardness, ductility (malleability) and fatigue resistance.
Fine-grained structures improve deformability and fatigue resistance, while coarse grains can impair mechanical properties. Controlling the grain size is therefore a critical aspect of quality assurance in order to fulfil the specified properties and ensure reliability in safety-critical applications.
Grain size in metals and grain size determination
The grain size in metals refers to the dimensions of the individual crystals that make up the metal structure. These microscopic crystals, also known as grains, are formed during the solidification and further processing of the metal.
The size and distribution of these grains have a profound effect on the physical and mechanical properties of a metal, such as strength, hardness, ductility and fatigue resistance. A finer grain structure generally leads to improved properties, which is of great importance for many industrial applications.
Grain sizes in QA for cold-rolled strip production
Grain size plays a key role in quality assurance, as it has a decisive influence on the mechanical and physical properties of metal products. A controlled and optimised grain size makes a significant contribution to achieving the desired physical and mechanical properties.
In processes such as cold-rolled strip production, where precision and reliability are crucial, precise control of the grain size enables the manufacture of products that can withstand constant stress while remaining mouldable.
Monitoring the grain size is therefore an integral part of the quality control processes. It helps to ensure compliance with industry standards and specific customer requirements.
Durch die kontinuierliche Überwachung und Anpassung der Prozessparameter können Hersteller sicherstellen, dass ihre Produkte die erforderlichen Spezifikationen erfüllen und eine gleichbleibend hohe Qualität bieten.
Grain size control is therefore not only a technical aspect of metal processing, but also a decisive factor for customer satisfaction and market reputation.
Tools and techniques for grain size measurement
There are various methods for determining the grain size in metals.
One of the most common methods is microscopic examination, in which the metal is viewed under a microscope and the grain sizes are measured directly or estimated using comparative images.
Other important methods are X-ray diffraction for non-destructive analysis of the internal structure and stresses, and electron microscopy for detailed analyses with high resolution.
These instruments are used systematically in the production process to continuously monitor grain size and distribution and ensure quality. The collected data is analysed, often using specialised software, to identify trends and deviations, which is crucial for process optimisation and quality control.
Measurement results and comparison with industry standards
After the grain size measurement, the results are presented using microstructure images, graphs and distribution tables, which show the grain size distribution and properties. Analysing this data requires expertise in materials science in order to evaluate the homogeneity, grain size and their influence on the mechanical properties.
An important step is to compare the results with industry standards from organisations such as ASTM or ISO, which define grain size requirements. This comparison helps manufacturers to assess the conformity of their products and shows necessary adjustments in the manufacturing process to optimise the grain size.
In some cases, the results can also be used to exceed existing standards and create a product of even higher quality. This comparison is crucial to ensure competitiveness in the market and to guarantee the reliability and safety of the end products.
Challenges with grain size measurement
Determining grain size in metals presents several challenges. One of the main issues is ensuring the accuracy and consistency of the measurements, as the grain size and distribution can vary throughout the material.
This requires representative sampling and careful preparation in order to achieve meaningful results. In addition, the interpretation of the data can be complex, especially when different grain shapes and orientations are present. The use of traditional microscopic methods can be time consuming and requires specialised personnel.
Several approaches can be taken to improve measurement accuracy and process control.
The use of automated and digitised microscopy systems with advanced image analysis software can increase the efficiency and accuracy of grain sizing. Systems such as MiViA enable fast and precise analysis of large sample areas and reduce human error in data interpretation.
Best Practices and Innovations
Presentation of industry-leading practices and the latest technological developments
Industry-leading practices and technological developments have been established in the metal industry, which contribute significantly to increasing efficiency and quality in production.
Particularly noteworthy is the use of AI-supported analysis tools that can process large amounts of data from the manufacturing process and recognise patterns in order to suggest process optimisations and improve product quality.
The digitalisation of the entire value chain, from procurement to production and delivery, is a key aspect of modern industry-leading practices.
By implementing Industry 4.0 concepts, including the Internet of Things (IoT) and integrated data platforms, companies can increase their efficiency, improve product quality and respond more quickly to market demands.
These developments show that continuous innovation and adaptation to new technologies are crucial to success in the fast-moving and highly competitive metal industry.
Summary
The analysis of grain size measurement in cold-rolled strip production has produced the following key findings:
- Firstly, the grain size is a decisive factor for the mechanical properties of the end product, with a finer grain structure leading to increased strength and ductility.
- The integration of automated microscopy systems and AI-supported analysis tools offers significant advantages for the accuracy and efficiency of grain size analysis.
- For the industry, it is advisable to invest in modern measurement technologies and provide ongoing training for staff to promote a deep understanding of material science and the effects of particle size.
- Continuous adaptation to new technological developments and the digitalisation of production processes are crucial to securing competitive advantages and being able to respond effectively to changing market requirements.
- Ultimately, quality assurance is a dynamic process that requires continuous attention and innovation in order to meet and exceed the high standards of cold-rolled strip production.